Lean開発思想の起源:トヨタ生産方式との関係をやさしく紐解く
Leanソフトウェア開発の背景には、製造業の知見があります。この記事では、その起源となったトヨタ生産方式との関係をたどりながら、Lean思想がソフトウェア開発にどう応用されているかを解説します。
「Lean開発って、結局なにがLeanなの?」
「なんでソフトウェアの話で“トヨタ”が出てくるの?」
そんな疑問を持ったことはありませんか?
実は、Leanソフトウェア開発の根っこには、**日本の製造業──特にトヨタ生産方式(TPS)**の知恵が深く関わっています。
この記事では、その関係性をわかりやすくひもときます。
Leanとは何か?一言でいうと「ムダをなくす」
Lean(リーン)は、文字通り「痩せた・無駄のない」という意味。
製造業の現場で、資源・在庫・工数・手戻りなど、あらゆるムダを削る思想として確立されました。
その思想をソフトウェア開発に応用したのが、Leanソフトウェア開発です。
トヨタ生産方式(TPS)とは?
TPSは、“必要なものを、必要なときに、必要な分だけ”つくるという原則のもと、
- 在庫を最小化し、
- 工程を平準化し、
- 改善を現場で繰り返す
という考え方を軸にした生産方式です。
🧱 代表的なキーワード
概念 | 説明 |
---|---|
ムダの排除 | 付加価値を生まない作業は削減対象とする |
ジャストインタイム | 必要なものを、必要なときに、必要な分だけつくる |
自働化(ニンベンのある自動化) | 異常があれば自動停止し、人が判断できる仕組み |
カイゼン | 改善は現場の日常的な営みである |
それがなぜソフトウェアに応用されたのか?
製造と開発、一見まったく違うように見えますが、実は共通点があります。
製造業 | ソフトウェア開発 |
---|---|
工程が複数に分かれている | 要件定義・設計・実装・テストなど |
変化に弱いとムダが増える | 仕様変更による手戻りが発生 |
現場の改善が成果を左右する | チーム内プロセスの改善が影響大 |
Lean開発は、この共通性に着目し、
**「ムダをなくし、継続的に学び、より早く価値を届ける」**という方向性を打ち出したのです。
『Lean Software Development』で整理された7原則
Mary & Tom Poppendieck夫妻の著書
『Lean Software Development』では、TPSをベースにしながらも、
ソフトウェアに適した7つの原則が再定義されています。
✅ 7つの原則
原則 | 内容 |
---|---|
ムダをなくす | 本質でない作業・中間成果物を最小化する |
学習を強化する | ドキュメントより経験、早いフィードバックを重視 |
決定を遅らせる | 不確実性の高い領域では、情報が揃ってから判断 |
できるだけ早く届ける | 顧客に早く価値を見せ、学びにつなげる |
チームを尊重する | 自律・信頼・現場の判断を尊重する |
全体を最適化する | 部分効率より、フロー全体のスムーズさを重視 |
品質を作り込む | 最初から品質を高める(テスト・リファクタリング) |
アジャイルやDevOpsとのつながり
Leanは、アジャイルやDevOpsと方向性を共有しています。
共通点 | 解説 |
---|---|
フィードバックループを重視 | 小さなサイクルで学び、調整する |
自律的なチーム | 上からの指示ではなく、現場の意思を尊重 |
継続的改善 | カイゼンとふりかえりの文化 |
Lean導入ステップ図(文化的段階モデル)
ステップ | 説明 | 実践例 |
---|---|---|
1. ムダに気づく | 無意味な会議、ドキュメント、レビュー待ち…に気づくことから始まる | 「これ、誰が使ってるんだっけ?」と問いかける |
2. 小さな改善を試す | 書き方・伝え方・プロセスの省略などを実験 | タスクの流れを見直す/Slack投稿テンプレ導入 |
3. 改善を仕組みにする | うまくいったものを仕組み化/テンプレ化 | 毎週ふりかえりで改善提案を話すルールを設ける |
4. チームで学び合う文化へ | 自律的に学び・改善し合う雰囲気が生まれる | 「これは改善ポイントかも」と誰でも言える |
5. Leanが“空気”になる | ツールでも施策でもなく、価値観として根づく | 変化に柔軟で、必要最小限が自然に保たれている |
まとめ:Leanは「考え方」であり「文化」である
Lean開発は、ツールやテンプレートではありません。
それは、「どうつくるか」ではなく「どう考えるか」の話。
- 価値を早く届けるにはどうしたらいいか?
- 本当にムダになっているものは何か?
- チームで改善する仕組みはできているか?
Leanの原点はトヨタですが、その精神は、どんなチームでも活かすことができます。
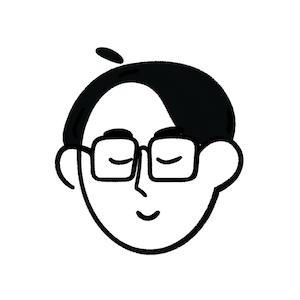
編集部